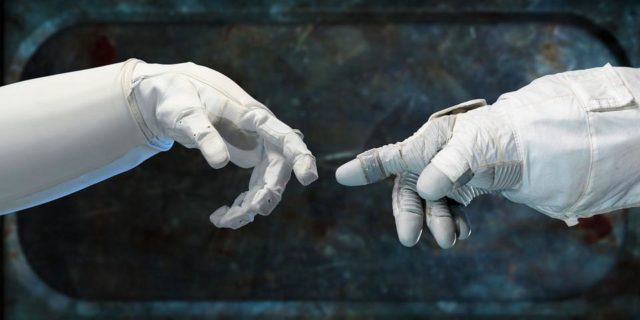
In 1980, Japan was the first to put the production of robots on a commercial basis. Since then, the demand is constantly growing. Thanks to artificial intelligence, modern robots are able to independently learn new skills necessary to solve tasks, gradually performing an increasing amount of routine work.
Currently, robotics, which, according to forecasts, should become the basis of the fourth industrial revolution, is undergoing another stage of rapid development. With artificial intelligence, new generations of robots are no longer as dangerous to humans as industrial machines. Today, collaborative robots (CoBots) are actively integrated into society, helping people in a variety of areas. Combining into the information networks, these devices are able not only to transmit information about changes in working conditions but also to teach other devices new acquired skills.
One of the main parts of any robot is the actuator, without which it will not be able to perform any action. Theoretically, you can use any type of actuator – hydraulic, pneumatic, piezoceramic, “air muscles” and others-but the most widespread actuators based on electric motors. Linear actuators can perform the rotational or linear motion, aimless motion or precise positioning (stepper motors), however, even micro actuators, have at least one winding in which it is necessary to form and maintain a current of a given value. For more details click here. If there are several such windings, as, for example, in brushless or stepper actuators, the currents in the windings must be formed according to a strictly defined algorithm. Thus, the control of the robot actuator turns into a rather serious technical problem, which is very difficult to solve without the use of modern power semiconductor devices and microcontrollers.
A modern robot can be defined as an autonomous system capable of performing certain tasks without human intervention. Despite the potentially unlimited scope of application, the number of practically used robots to date is still small, and the number of their types – even less.
Robotic assistants (picture 1) are designed to perform a specific task, such as cleaning a room or mowing lawns.
Industrial robots are old-timers among the devices of this class. They perform most of the routine operations in the production, and the first of them have already worked more than 100 thousand hours and continue to operate until now. Most industrial robots are manipulators with a minimum number of sensors and degrees of freedom (picture 2), capable of autonomously performing only certain, pre-programmed actions.
Warehouse rectangulars (picture 3), which include both automatically controlled vehicles and automated warehouse systems, are similar in the complexity of the control algorithms used to home assistant robots, only, unlike the latter, they are larger, more powerful and more accurate.
Collaborative robots (CoBots) are the most complex type of robots, because they, unlike other mechanisms, have to cooperate with people (picture 4). A good example of a CoBot is a robotic arm, whose main purpose is to help a person move small objects and perform simple operations.
Robots will become an integral part of our lives in the very near future. Freeing a person from routine work, they are gradually but steadily introduced into all spheres of human life.
It is obvious that the requirements for the accuracy of robot movements, and therefore – to the technical characteristics of the actuators every year will only increase. It is possible that in the future it will be necessary to abandon simple collector engines, because, for example, the level of noise created by them may be too high. Perhaps the control algorithms for brushless motors will be standardized, and there will be a need to implement them at the hardware level. In any case, Progressive Automations will follow the development of this area and offer high-quality solutions that allow in a short time to design micro actuators that meet the highest standards.