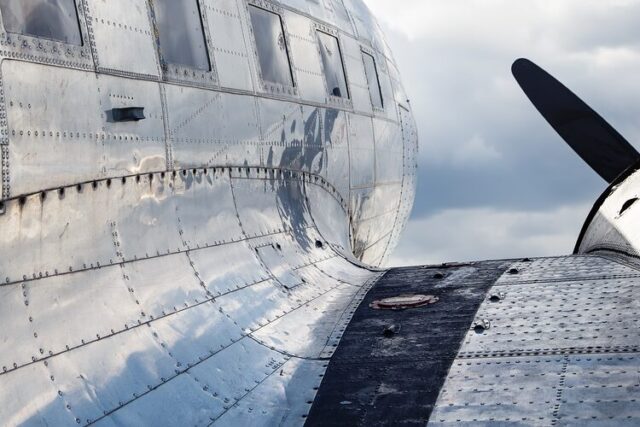
We come into contact with aluminum every day. Every time we turn around, it seems like there is another item made of aluminum; examples include the foil used to cover food, the ladder used to clean gutters, the screen door used to keep flies out, and the golf clubs used for a round of golf.
But have you given any regard to the aluminum-made metal things that are currently in the air? Yes, we are discussing aircraft. What type of aluminum is used in their construction?
Undoubtedly, not all aluminum is created equal. You must that the highest grade of aluminum was used in the construction of the aircraft the next time you board one.
Aluminum and its alloys are powerfully resistant to corrosion. The sensitivity of these alloys to high temperatures ranging from 200 degrees Celsius to 250 degrees Celsius make them to be considered as good low-temperature alloys. When exposed to subzero conditions, their strength grows, while the strength decreases when subjected to warm temperatures and even in some cases the strength is lost.
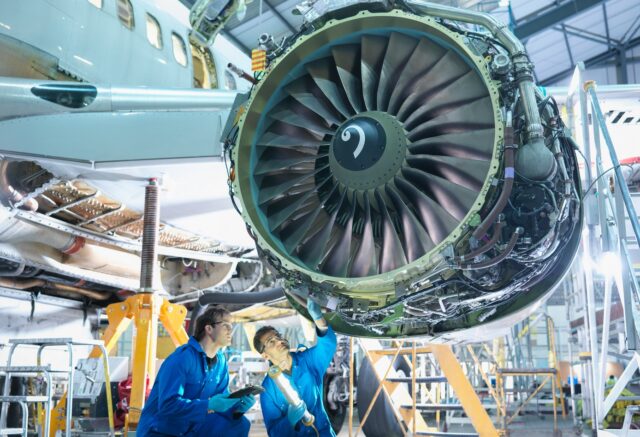
Aluminum for the aircraft industry
Ultra-high-strength deformed aluminum alloy, or aircraft aluminum alloy is being utilized extensively in the aviation sector. Aerospace aluminum alloys must meet higher standards for strength, hardness, toughness, fatigue resistance, and plasticity than standard aluminum alloys. Aerospace aluminum alloy has excellent mechanical and processing characteristics, good plasticity following solution treatment, good heat treatment strengthening effect, high strength, and excellent toughness. It is the perfect structural material for flying. 2024 aluminum sheets and 2024 aluminum extrusion products are widely used in aircraft industry.
Properties of 2024 Aluminum
A common duralumin alloy (Al-Mg-Cu aluminum alloy) containing four and a half percent copper, 0.6% manganese, and one and a half percent magnesium is aluminum alloy 2024. It performs well overall and has a reasonable composition. Additionally, 2024 aluminum has excellent strength, and some heat resistance, and can be utilized as working components below 150 °C.
The main constituent that take part in the manufacturing of aluminum 2024 is copper. Aluminum 2024 exhibits high strength-to-weight ratio and strong fatigue resistance, which make them considered as its primary applications. Besides, it is capable of being welded, but only when friction welding is used.
After being heat-treated to a temperature between three hundred ninety-nine and four hundred twenty-seven degrees Celsius for almost two hours. Afterward, using a furnace, aluminum alloy 2024 is gradually cooled down. Alternately, aluminum alloy 2024 can be annealed at three hundred forty-three degrees Celsius for the same amount of time. It can, in between cold working operations, be cooled down in the air.
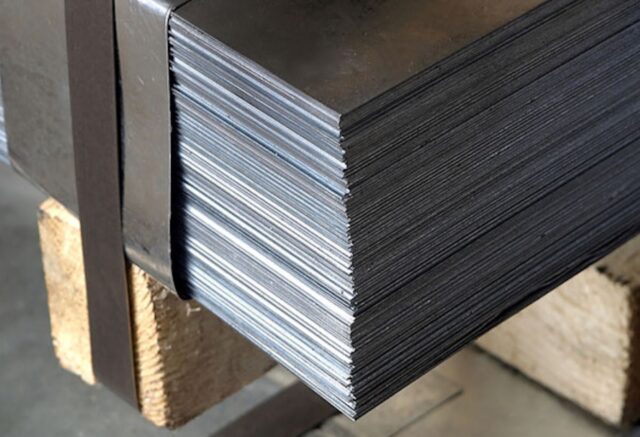
Fatigue resistance
2024 aluminum is typically used for aircraft structures because of its low density, high strength, and resistance to corrosion in the aviation sector. As maneuverability and speed requirements for aircraft have increased in recent years, the aircraft will experience increasingly complicated load spectrum impacts.
The aircraft’s fatigue life is estimated to be 100,000 flight cycles under the condensed gust load spectrum M1 and M2, demonstrating the aluminum alloy 2024’s good fatigue performance and suitability as an aerospace material for repeated tension and compression loads.
Machinability and Forming
The 2024 alloy may be machined well in its heat-treated and tempered state. Additionally, the alloy might not be hot formed. Ideal for applications requiring structural strength and fatigue resistance is aluminum 2024. 2024 aluminum plate is available from 1/4 inch to 6 inches thick. These plates can be used in a variety of applications, such as hydraulic manifolds, tension members, ribs, and shear webs.
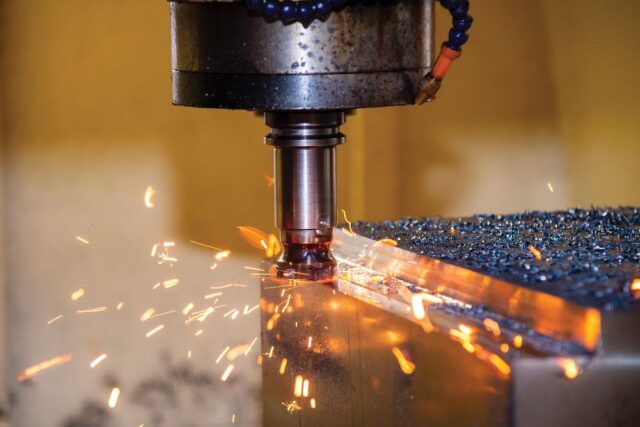
Corrosion Resistance
More susceptible to corrosion than the majority of other aluminum alloys is the 2024 alloy. Manufacturers have solved this problem by applying a coating of corrosion-resistant metal to these vulnerable alloys. The most common application of this coat, which can occasionally be high purity aluminum or another alloy, is in clad sheet metal, where the primary alloy can be layered between the layers of cladding. Products made of clad aluminum have been created to provide corrosion-resistant alloys like 2024 with the best possible result. This innovation makes 2024 aluminum particularly beneficial since it may be used in places where the naked alloy would typically deteriorate due to its strength.
Benefits of Aluminum 2024
2024 has the qualities that make it perfect for hydraulic cylinders, constructions, hardware, transportation components (truck wheels, for example), and other uses that can profit from strong fatigue resistance in addition to having a high yield strength of 50,000 psi. For several military and aviation applications that involve extremely high temperatures in the engine areas, an aluminum 2024 sheet is the best option. The exceptional machinability of aluminum 2024 allows for flash, spot, or seam welding. It is heat treatable and has good working qualities. It is possible to extrude this alloy and get it as sheets and plates.
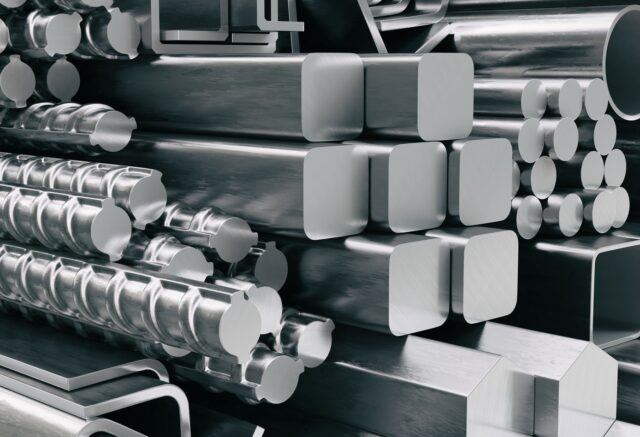
The three main advantages of using aluminum 2024 in airplane construction are as follows:
- It is portable. The application of aluminum in the manufacturing of an airplane reduces its weight appreciably. The weight reduction not only keeps the airplane flying for long but also causes an increase in the fuel efficiency and helps in carrying huge loads.
- Aluminum is incredibly corrosion-resistant, which is vital in preserving the integrity of an airplane’s architecture while it flies through a range of conditions.
- Aluminum’s strength makes it a perfect alternative for heavier metals.
Wrap Up
The 2024 aluminum alloy’s excellent strength and resilience to fatigue make it a popular choice for structural applications in airplanes. It is less adaptable than 6061 but stronger.
Due to its adaptability, aluminum 2024 is widely used in the aircraft sector to build more dependable and affordable aircraft. Aluminum will always be valued as long as people are flying through the air.
Therefore, keep in mind that the primary characteristics of aircraft-grade aluminum are its light weight, strength, and corrosion resistance the next time you hear the term. These characteristics make aluminum 2024 beneficial in numerous applications as well as crucial to the safety of the airplane.